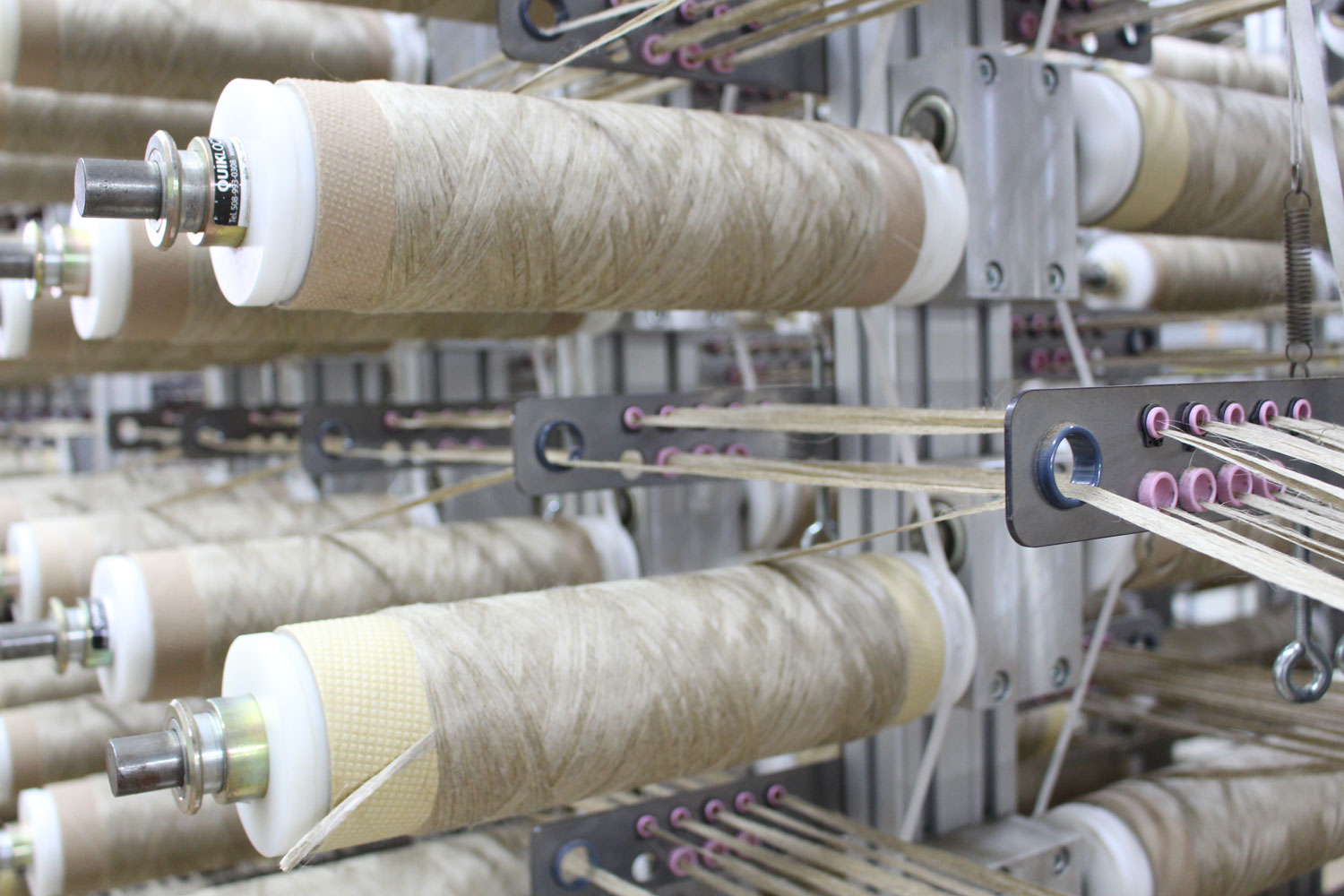
Bastfaserpflanzen, wie die bekannten einheimischen Arten Flachs/Lein, Hanf und Nessel, dienten über Jahrtausende als Grundlage für die Gewinnung von Fasern. Aus den Fasern wurden unterschiedlichste Produkte hergestellt: Bekleidung, „technische Gewebe“ wie z. B. Säcke und Segel, Taue und Netze, usw. Weiterhin bekannte Anwendungen sind Dichtmaterialien wie „Kalfaterband“ zur Fensterabdichtung oder „Dichthanf“ zum Abdichten von Rohrgewinden von Wasserleitungen. Ihre Bedeutung verloren sie insbesondere im Textilsektor mit dem „Siegeszug der Baumwolle“ (die auch Aufgrund ihres Aufbaus einfacher und Anlagentechnisch effizienter versponnen werden kann als die deutlich längeren Bastfasern) und der Erfindung erdölbasierter Synthesefasern, den sog. „Kunstfasern“.
Mit wachsenden Kenntnissen um den Aufbau von Bastfasern und vor dem Hintergrund der Bioökonomiestrategie gewinnen einheimische Bastfasern indes zunehmend an Bedeutung.
Die beiden annuellen Bastfaserpflanzen Flachs und Hanf tragen zur Erweiterung der Fruchtfolgen bei und leisten einen wesentlichen Beitrag sowohl zum Erhalt und Steigerung der Bodenfruchtbarkeit als auch Verringerung des Schädlingsdrucks. Zwar stehen sie grundsätzlich im Wettbewerb zum Anbau von Nahrungs- und Futtermittelpflanzen, bei ganzheitlicher Betrachtung überwiegen jedoch die Vorteile. In diesem Zusammenhang sind Bestrebungen zu nennen, vor allem Hanf als Zwischenfrucht (d. h. nach der Ernte z. B. von Winterweizen und vor der Aussaat von Sommergetreiden im Frühjahr anzubauen, woraus positive Effekte wie z. B. Vermeidung von Bodenerosion und Konkurrenz zum Getreideanbau resultieren). Und das schnelle Wachstum von Hanf führt dazu, dass bei seinem Anbau auf Pflanzenschutzmaßnahmen verzichtet werden kann.
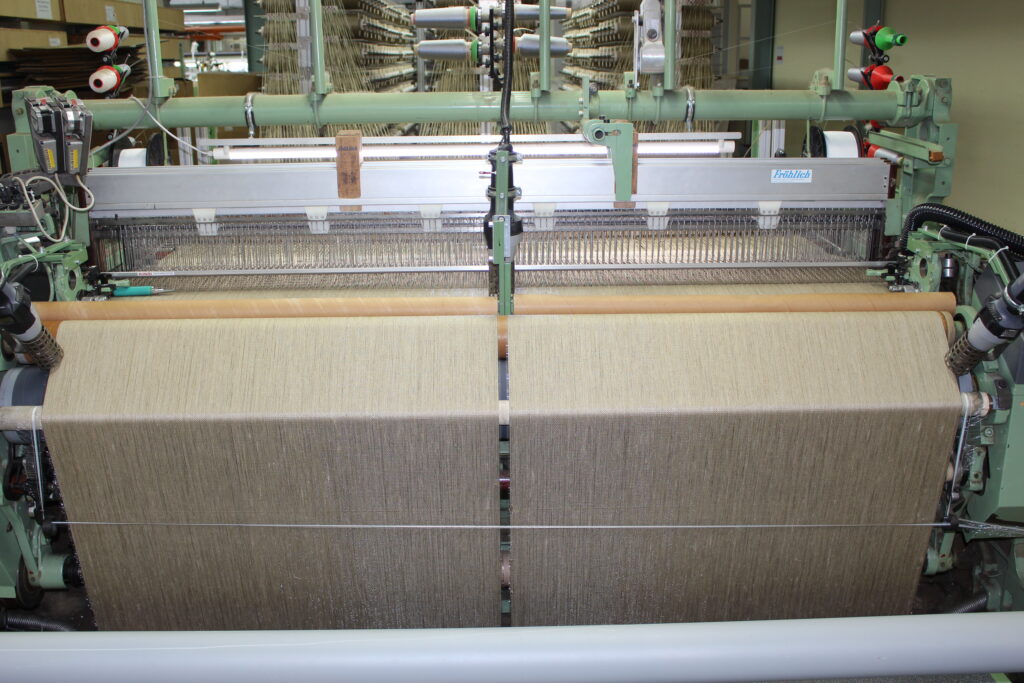
Moderne Erzeugungsprozesse erlauben die effiziente Fasergewinnung und bieten darüber hinaus Möglichkeiten selektiver Nutzungen. Aktuell sind Bastfasern aus einheimischen Faserpflanzen in technischen Produkten, sog. „Vliesen“ (engl. non-woven) etabliert. Hervorzuheben ist ihr Einsatz in der Automobilindustrie, wo sie die Grundlage für die Herstellung von Formbauteilen für den Fahrzeuginnenraum (z. B. Türinnenverkleidung, Kofferraumboden, „Hutablage“, Sitzverkleidung) bilden. Aber auch im Dämmstoffbereich haben sie sich ihre Nische erobert. Im Bekleidungs-/ Textilsektor sind vor allem Flachsfasern (Synonym „Leinfasern“) etabliert; Nischenanwendungen in diesem Bereich erobern sich aktuell erfolgreich Hanf- und Nesselfasern.
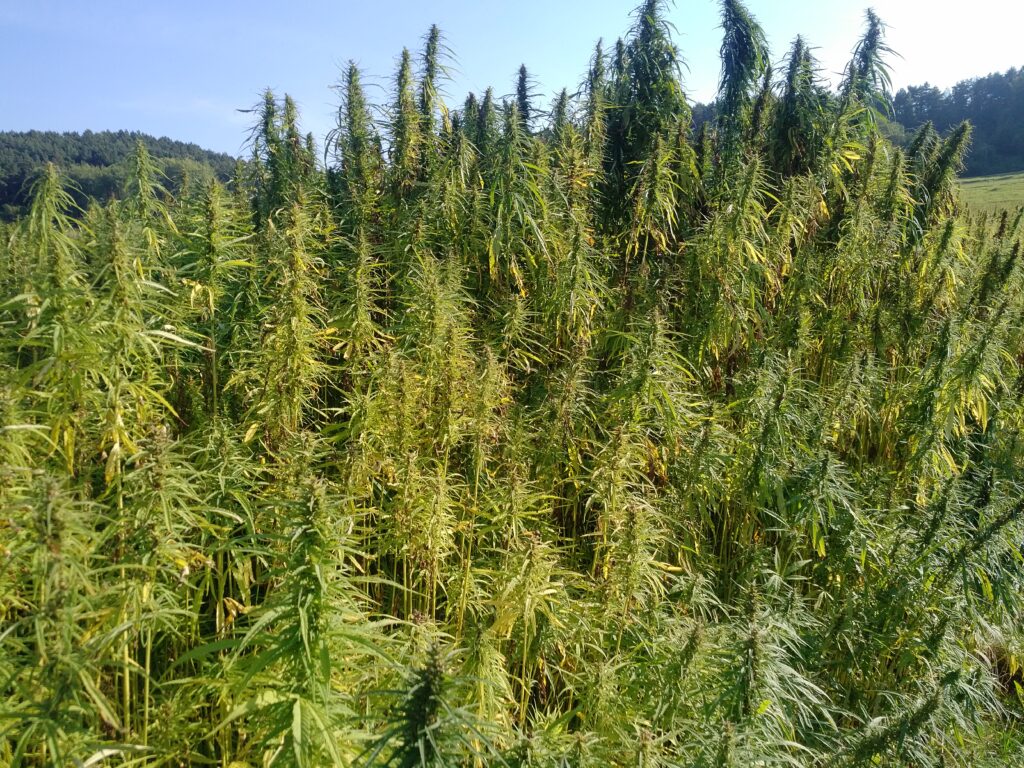
So sind Bastfasern aufgebaut
Bastfasern bestehen aus Faserzellen („Elementarfasern“), die längeren Fasern („Technische Fasern“) bilden. Sie formieren sich zu Bastfaserbündeln, die im äußeren Radius der Pflanze den Stängel gegen Zugkräfte stabilisieren. Die Verbindungen erfolgen im Wesentlichen über Zuckermoleküle („Pektine“) und Lignine. Entscheiden für die Festigkeit der Faserbündel ist die Anzahl der Elementarfasern eines Bündels sowie die Festigkeit der einzelnen Komponenten über Pektin- und Ligninverbindungen.
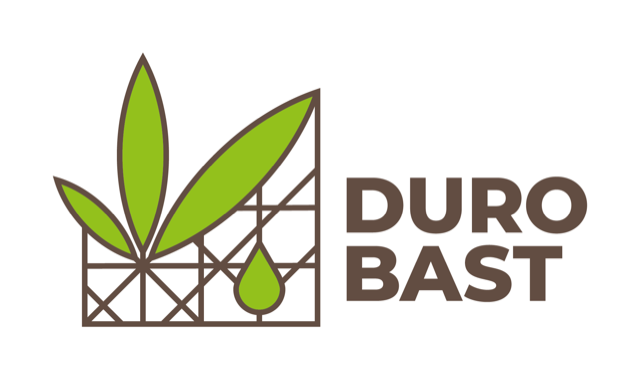
Diese Rolle spielt DuroBast
Die interessanten technischen Potentiale von Bastfasern erfahren gegenwärtig Beschränkungen, die sich aus ihren hygroskopischen Eigenschaften („Feuchtigkeitsaufnahme“) und Festigkeiten (inbes. auf Ebene technischer Fasern und Faserbündel) ergeben. Diesem Problem widmet sich DuroBast: durch die Polymerisation von Monomeren in den kleinen „Vertiefungen“ („Höhlen“/„Cavitäten“) der Elementarfasern werden diese gegen das Eindringen von Wasser/Feuchtigkeit geschützt („imprägniert“); gleichzeitig bieten die anschließend verknüpften („polymerisierten“) Monomere Möglichkeiten zur Steigerung der Festigkeit („Consolidierung“) zellulärer Faserelement-Strukturen.